JDR Cable Systems (JDR), the global subsea cable supplier and service provider, a part of the TFK Group, has achieved several significant milestones in the construction of its new £130 million state-of-the-art subsea cable manufacturing facility in Cambois, near Blyth, Northumberland.
The facility will expand the product offerings of both JDR and TFKable, including high-voltage and extended-length land and inter-array cables. The manufacturing capabilities of both land and subsea cables will provide the offshore energy market with a comprehensive offering to meet the varied requirements of the industry.
It positions the TFKable Group’s facility as a unique hub in the UK, capable of comprehensive manufacturing of subsea and land cables used to connect offshore wind farms to the energy grid.
The project is supported by His Majesty’s Government and the Secretary of State as part of the DESNZ Offshore Wind Manufacturing Investment Support Scheme. Significant advancements have been made in the facility foundation work, including the successful placement of over 150 building pad foundations and the erection of a substantial portion of the steel frame for the main hall, enhancing the facility’s structural integrity. Roofing and cladding works have also commenced as construction continues at pace.
Notably, all piling for the foundations of the Vertical Lay-up Machine (VLM) and Continuous Catenary Vulcanisation Towers (CCV) have now been completed. The towers are supported by a total of 250 piles drilled to a depth of 24m below ground level to reach bedrock and provide the essential support for the advanced machinery housed within them. Once operational, the CCV line will establish the site as the only facility in the UK capable of full start-to-finish manufacturing of high-voltage subsea cables. These cables are required for offshore wind farms and to enable the subsea energy infrastructure which is essential for the growing global renewable energy market.
A crucial application of the facility will be the production of high and extra-high voltage cables at 132kV and above. These will enable the operation of larger turbines offshore, allowing the connection of more power back to shore. With the facility foundation work nearing completion and over 1700 tonnes of concrete foundations now having been poured, the project is on course to meet the significant increase in demand expected for high-voltage cables in the middle of the decade.
Machinery deliveries for the facility are also progressing, with complex, high-quality European manufactured machines already completed and ready for installation, which will take place once the building is sealed, and floor slab completed in coming months.
Reacting to the milestones, James Young, Chief Strategy and Compliance Officer at JDR Cable Systems said:
“We are proud to contribute to the growth of the renewable energy sector and the UK’s position in offshore wind manufacturing. Constructing this first-in-class facility in the UK enhances our ability to produce high-quality, high-voltage subsea cables, that we know will be essential in meeting the demands of not only the offshore renewable energy market, but also the wider needs of the energy sector as we seek to decarbonise our energy system and achieve net-zero emissions by 2050.”
Supporting JDR to minimise the environmental footprint of the project, construction work has reused existing foundations from the former Blyth A&B coal power station on-site, reducing the emissions related to this stage of construction. As well as providing local employment opportunities in the energy sector, local construction and logistics supply chains have been actively supported through the procurement of steelwork and cladding materials, and the use of specialist groundworks and piling contractors.
Reflecting further on the project, Young continued:
“As a proud UK-based company, it’s vital that we contribute to the local economy of the North East and the UK more widely, supporting local workforces and strengthening our supply chains as we bring our facility online to help to lead the energy transition here in the UK and beyond.”
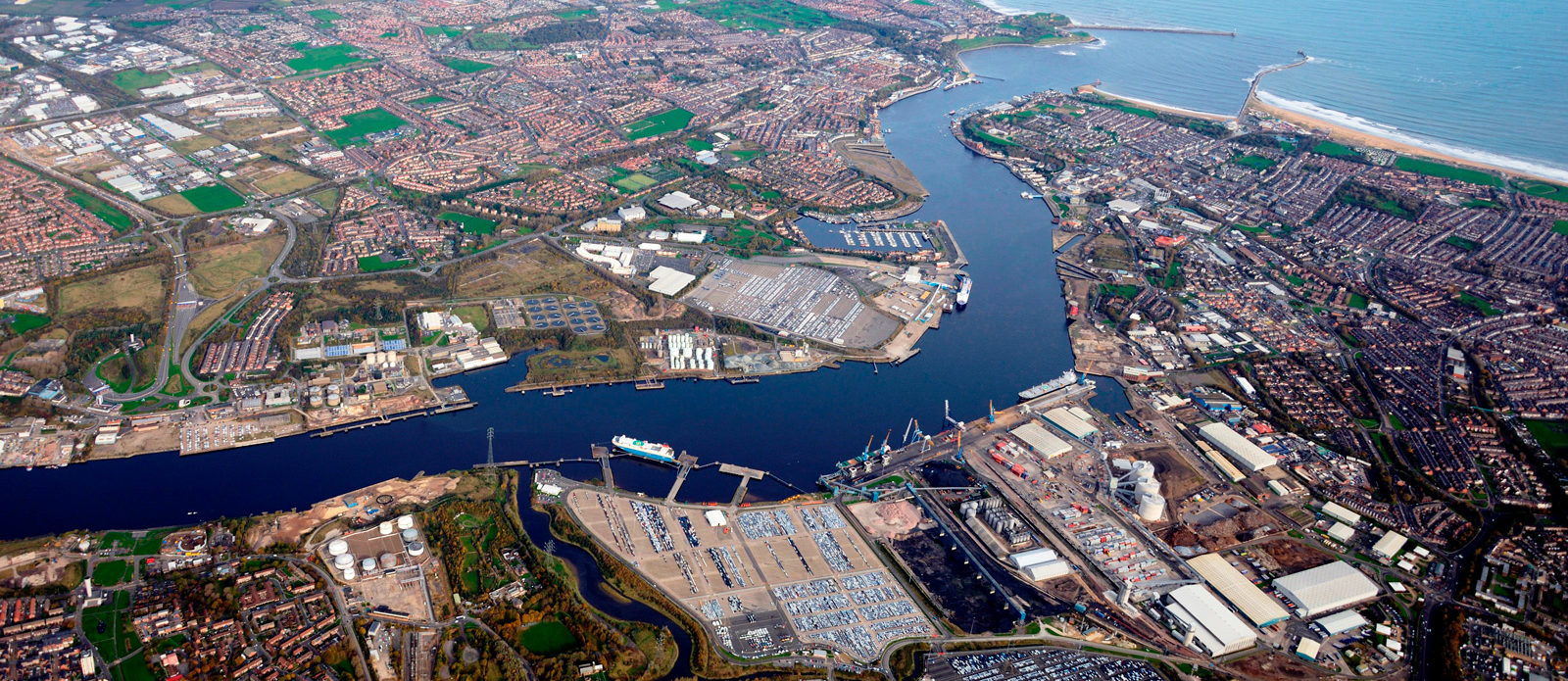